Quite a few things can happen to the hydraulic fluid that powers your compact equipment, including contamination and aging. Even if you don’t have a fleet of equipment you’re responsible for, you still need to know the basics about hydraulic fluid analysis. To that end, here are answers to five commonly asked questions about hydraulic fluid analysis.
Here are a few other blog posts you might be interested in ...
- Hydraulic Drive Motors and Contamination
- Hydraulic Contamination Issues in Newer Machines
- Abrasive Contamination and Final Drive Motors
Hydraulic Fluid Analysis FAQs
1. Why Should I Bother with Fluid Analysis?
There are several reasons why fluid analysis is a good idea, but these reasons are dependent on making smart use of your fluid analysis data. When you use this data properly …
- It allows you to detect when things are beginning to go wrong and address problems before they lead to expensive repairs or catastrophic failure
- It can assist you in troubleshooting existing problems
- It can aid you in reducing downtime and increasing MTBF (mean time between failures)
- It can increase the useful life of your equipment
- It can help you reduce M&O costs
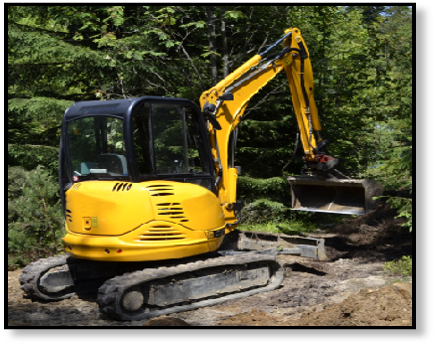
2. What Does Fluid Analysis Tell Me?
Fluid analysis provides information about the condition of your hydraulic fluid (e.g., has it aged to the point that it needs to be replaced), its level of contamination (e.g., size distribution, type), and whether there are signs of abnormal wear (e.g., presence and composition of wear debris).
3. What Kind of Data Can I Get From Fluid Analysis?
So, what kind of data can you get from fluid analysis? That depends heavily on the analysis techniques used. Here are four of the most common ones:
- Particle distribution: this test gives you a summary of the number of contaminant particles, classified by size
- Proton induced X-ray: this test, also known as PIXE, provides a summary of elemental composition of wear debris and solid contaminants in your hydraulic fluid
- Water content: this test will tell you how much water is present in the sample
- Gravimetric: this test is similar to the particle distribution test in that it can provide information about the presence of particles above a certain size, but it can’t tell you anything about the size distribution
- Ferrographic wear debris: this test uses magnetic fields to assess the presence of wear materials in your sample
4. When Should I Test Hydraulic Fluid?
Your equipment manufacturer will provide information about when hydraulic fluid testing should be performed. If the hydraulic system (or a component within it) suffers a catastrophic failure, if you have reason to believe the fluid has been contaminated, or you’ve recently performed a repair or maintenance, you should have an additional analysis run outside of the recommended schedule.
5. Where Should I Pull a Fluid Sample From?
Where you pull a hydraulic oil sample depends on what kind of information you are trying to get from performing an analysis. For general analysis, you should pull the sample from what is known as the primary sample location: immediately upstream of the return filter. If you are checking for wear debris from a particular component then you need to pull a sample from the discharge before the fluid encounters a filter.
Conclusion
Here are Texas Final Drive, we know how much damage contamination can do to a final drive motor -- and it always saddens us to see an otherwise good travel motor destroyed by contamination. We always encourage our readers -- including you -- to keep up the maintenance on your drives and watch out for contamination. Even if you fluid analysis isn't in your budget, there are things you can do to minimize contamination.