We've talked about foaming hydraulic fluid, but what if it's cloudy? Then your problem is water contamination. Read on how to learn its effects, how it gets in, how to remove, and how to prevent it.
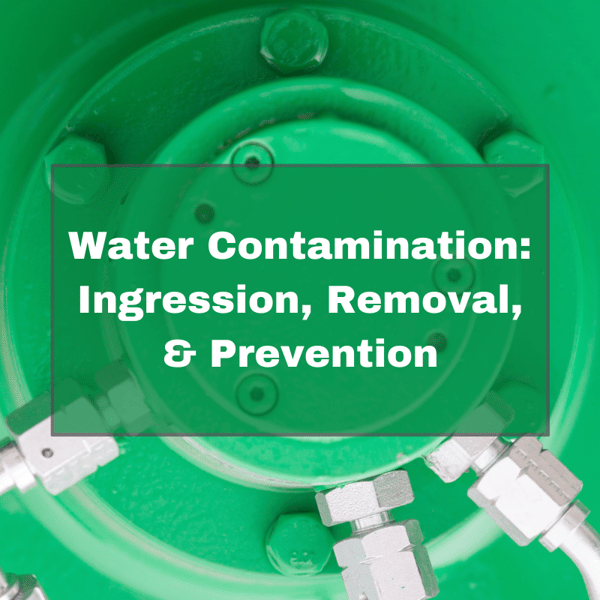
Here are a few other blog posts you might find of interest:
- Preventing Hydraulic Contamination
- Hydraulic Contamination Issues in Newer Machines
- Very Real Dangers of Reactive Maintenance
Water and Hydraulic Fluid
Water is the most common form of hydraulic contamination and is classified as chemical contamination. Certain levels of water (or moisture) contamination aren't problematic--but by the time your hydraulic oil looks cloudy, there are some problems about to develop.
Water Saturation Levels
Not unlike air contamination, there are three different levels of water contamination: dissolved in the hydraulics fluid molecular structure, free, and emulsified. Contamination always begins with water in its dissolved form. When there is too much water to be dissolved in the fluid we say that it is saturated. For water to be a serious problem, it has to be above saturation.
Water is good for your body, but not for your hydraulic system.
For mineral-based hydraulic fluid, saturation occurs when there is 200 - 300 ppm (parts per million) of water present. For synthetic hydraulic fluid, the limit is 1,000 ppm (0.1%). Once the saturation limit has been reached, hydraulic fluid starts to look cloudy because free water is now present in the hydraulic fluid.
Effects of Water Contamination
So why is water contamination bad?
It's going to make the fluid harder to filter and can actually clog the filters. It can make it easier for air to be entrained in the hydraulic fluid which can also lead to issues with cavitation.
The presence of water will impact the elasticity and strength of your hydraulic fluid, reducing the performance and efficiency of your system.
Lubricants (including hydraulic fluid) possess what is known as lubricant film strength. This property is related to how well a lubricant can protect critical surfaces. If that strength is reduced, this leaves key surfaces subject to corrosion and accelerated wear.
The presence of water can reduce the life of your bearings to 30% of what they should be, and that's with only 0.01% present (which isn't even above the saturation level).
Bearings are a critical component within your final drives and pumps.
The presence of moisture in your hydraulic fluid will significantly increase the chances of cavitation.
Water crystals can form in hydraulic fluid when the temperature drops below freezing, which can seriously compromise the performance of components like valves.
The presence of water can adversely affect some of the key additives in your hydraulic fluid. In some cases, it will deplete them or chemically reacts with them. The chemical reactions can lead to corrosive by-products such as acids, alcohols, and sludges.
The presence of water can also lead to rust, which you don't need to be told is really bad inside your hydraulic system.
Where Water Contamination Comes From
Water is a form of ingress contamination -- it has to make its way from the outside. It usually occurs when a hydraulic system operates in humid conditions if the reservoir doesn't have any built-in protection against it.
Water can also make its way into when the hydraulic system is open or if there is a leaking seal exposed to water or high humidity levels. The is the common way that water contaminates hydraulic fluid and is referred to as atmospheric ingress.
Your pumps and hydraulic motors have seals that should be replaced as soon as they begin to leak.
Also, keep in mind that even brand new hydraulic oil can have contaminants present. This contamination can occur during manufacture, processing, and storage. In fact, storage can be especially problematic even when hydraulic fluid is stored in a waterproof container. If that container experiences some drastic changes in temperature, it can "breathe in" moisture.
How to Remove Water Contamination
According to Parker, there are three basic ways to remove water from your hydraulic fluid:
- Polymeric filters, used to trap and absorb small amounts of water
- Vacuum distillation, which combines heat (at a temperature that won't damage the hydraulic fluid) and vacuum pressure
- Dehumidification, also known as a headspace flush, focuses on removing water from the headspace
How to Prevent Water Contamination
Most experts agree that the best (and cheapest) way to deal with water contamination is to prevent it. One method is to install a desiccant breather on the tank or to pass desiccant dry air through the reservoir. Also, keep in mind that reservoir breathers are a common way for water to enter a hydraulic system. An excellent way to minimize the chances of that happening is to replace your breather cap with a hygroscopic breather.
And now for some practical tips:
- Always store both new and old hydraulic fluid in a temperature-controlled atmosphere
- Keep hydraulic fluid containers closed when they aren't in use
- Don't allow water to collect on the top of fluid containers
- Keeps ports closed during repair
- Regularly maintain your filters
Conclusion
Here at Texas Final Drive, we encourage our customers to maintain and care for their drives -- even though it ends up costing us. We hate to see a machine that hasn't been cared for, and that includes final drive motors and hydraulic pumps that show signs of water contamination damage.