When a final drive has been pulled from a active machine, it is going to be a mess -- caked over with dirt or clay, smeared with gear oil and maybe the aftermath of a hydraulic leak, perhaps rusty in a few spots, and definitely in need of a good cleaning before it is opened up. In this Shop Talk Blog post, our topic is cleaning up that final drive inside and out. This should especially be of interest to hydraulics shops that may see quite a few final drives passing through their shop for maintenance on a regular basis.
Why Cleaning is Important
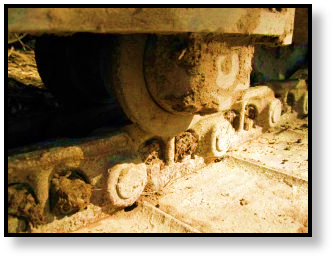
Hydraulic components, whether they are final drive hydraulic motors or main pumps, do not do well when exposed to contamination. Contamination can take quite a few different forms, including dirt, sand, grit, grease, and water. It is important not to introduce any additional contaminants to a hydraulic motor when disassembling it for maintenance or repair. What follows is a summary of how we clean final drives before we open them up, and how we clean the parts after they are removed.
Removal of External Buildup
When a final drive comes in for repair, it is typically caked in hardened materials. That is normal, because these hydraulic motors and final drives are going to end up covered in things like mud and clay just through regular use. That’s why one of the first things we do is get out an pneumatic needle scaler (also known as a needlegun scaler) to remove as much of this thick crust as possible. It also helps to remove a substantial amount of rust and scaling.
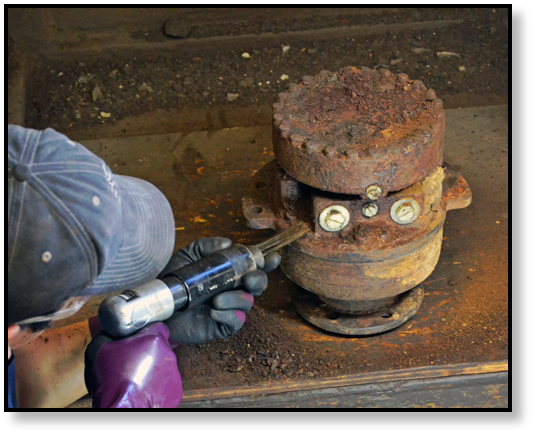
Wash Cabinet
The next step in our cleaning process is to place the final drive in an automated parts washer cabinet. The final drive is sprayed with high pressure, high temperature detergent to remove grease, oil, carbon, and similar contaminants from the surface of the final drive. Unlike a pressure washer, the parts washer cabinet is automated. The final drive is placed on a rotating platform, the door is closed, and the cycle is started. When the final drive is removed at the end of the cleaning cycle, it has been thoroughly cleaned and degreased. From here, the final drive moves on to the final step of external cleaning.
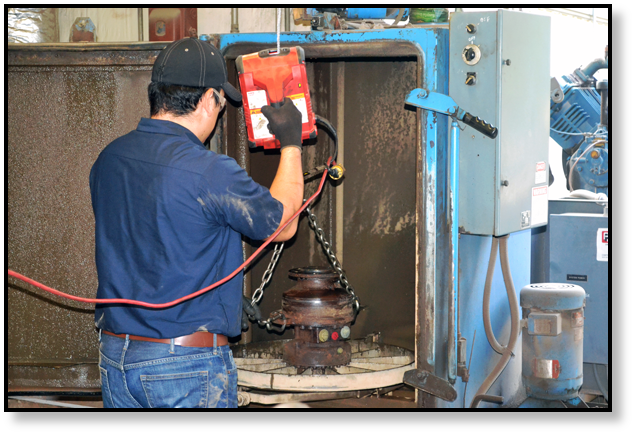
Sandblasting
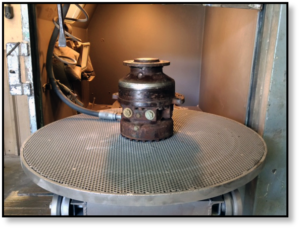
After the bulk of external buildup is removed and the drive has been thoroughly degreased, the hydraulic motor goes to the sandblasting cabinet. There, high pressure blasts of sand are used to dislodge the remaining crusted material. This process is also known as abrasive cleaning or abrasive grit blasting. Sandblasting also removes any external scaling, rust, paint, and any hardened materials that remain after using the needle scaler. In addition, it helps prepare the exterior of the final drive for a fresh coat of paint.
Dealing with the Parts
Only after the exterior of the final drive has been thoroughly cleaned will it be opened for evaluation and repair / rebuilding. Individual parts like gears, cam rings, and such are thoroughly cleaned. Parts have to be thoroughly cleansed of greases, oils, and other lubricants, as well as contaminants that may been introduced to the hydraulic system, before they can be properly evaluated. These parts are processed using a smaller parts washer like the one shown below.
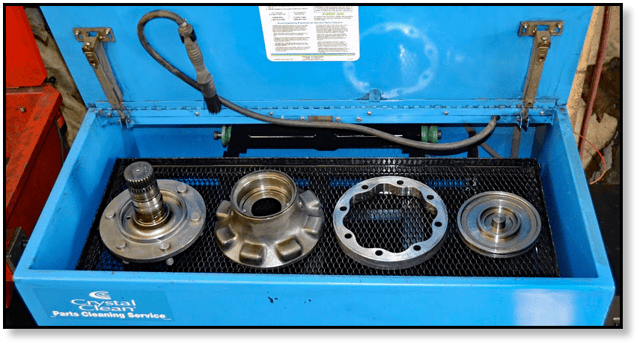
Conclusion
When its time to fix a final drive or perform maintenance on it (e.g., replacing seals or bearings, diagnosing problems), it needs to be cleaned up before it is opened. Hydraulic contamination is one of the number one causes of final drive failure, and it would be a shame to damage an otherwise good final drive through carelessness.
Texas Final Drive is your partner in providing new or remanufactured final drive hydraulic motors from a single mini-excavator to a fleet of heavy equipment. Call today so we can find the right final drive or hydraulic component for you, or check out our online store to find your O.E.M. manufacturer brand motor now.