How much do you remember about hydraulic pressure control valves? Read on for a quick review of types, uses, and hydraulic circuit symbols.
Here are some other Shop Talk Blog posts you might find of interest:
- Basics of Hydraulics, Part 1: Introduction to Pressure
- The Ultimate Glossary of Terms about Hydraulic Motors
- How Does an Axial Piston Final Drive Motor Work?
Hydraulic Pressure Control Valves
Pressure control valves are, as the name implies, used to regulate pressure within a hydraulic system. They are used when the pressure needs to be maintained within a certain range of levels, either as prescribed by the system manufacturer or determined by the individual operating on the system.
Pressure control valves are crucial because they prevent high pressure that can lead to leaks or damage to sensitive components. Burst pipes and hydraulic lines can result when there is no control valve in place to prevent excess pressure buildup.
Counterbalance Valve
You've probably noticed that a skid steer in good repair can keep a load lifted without dropping. When it comes time to lower it, it doesn't just BOOM hit the ground, but lowers in a controlled manner. A key component used to achieve this is the counterbalance valve, which which is used to keep a suspended load from dropping and to allow it to drop in a controlled manner. Or, in more general terms, these valves serve to either restrict movement or balance a load that a motor, pump, or cylinder is holding in place.
A special type of counterbalance valve is the brake valve. Brake valves are commonly used with hydraulic motors, including the drive motors on a SSL or CTL and hydraulic winch motors on cranes.
Pressure Relief Valves
A pressure relief valve is designed to open when pressure reaches a certain level and allow pressurized fluid to flow out of the system. This serves to restore the pressure at or below the maximum set pressure. These values go by several names, including safety relief valves, pressure safety valves, and safety valves. Pressure relief valves basically serve to kept the hydraulic system protected from extreme pressures.
Circuit Symbol for a Pressure Release Valve, Wikimedia Commons by MovGP0 / CC BY (https://creativecommons.org/licenses/by/3.0)
There are several types of pressure relief valves,with the three most common being direct-acting, direct-operated pilot type, and remote-actuated pilot type. The direct-acting pressure relief valves make use of a piston or spool acting against a heavy spring. Direct-operated pilot type relief valves have a piston acting against a small spring and are pilot operated; remote-actuated pilot relief valves are controlled by a remote pilot valve that may be connected to the relief valve via piping.
Reducing valves
A pressure reducing valve allows pressurized fluid to flow until a preset pressure is reached downstream from the valve. Once the downstream pressure reaches or exceeds this set pressure, it exerts pressure that forces the pressure reducing valve to throttle down the flow into that branch.
Circuit Symbol for a Reducing Valve, Wikimedia Commons by Snipre / Public domain
It is not uncommon to achieve a 1:10 pressure reduction with these valves and they are typically used for hydraulic systems where more than one operating system pressure is necessary for operation.
Sequence Valve
Sequence valves, also known as hydraulic sequencing valves, work very similar to pressure relief valves. The difference occurs after the set pressure has been reached: a sequence valve will divert the fluid to another part of the system (such as a hydraulic motor or a hydraulic cylinder). Basically they are used to set up a sequence of different operations and are available as either direct-acting or direct-acting pilot types. Direct-acting sequence valves are typically reserved for low pressure service, while the direct-acting pilot type valve is for higher pressures.
Circuit Symbol for a Sequence Valve, Wikimedia Commons by MovGP0 / CC BY (https://creativecommons.org/licenses/by/3.0)
Unloading Valves
An unloading valve is used to dump excess fluid, typically from a pump or accumjulator into a tank with little or no pressure. These valves are normally actuated from some type of external signal.
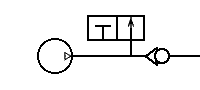
Circuit Symbol for am Unloading Valve, Wikimedia Commons by Vivan755 / CC BY-SA (https://creativecommons.org/licenses/by-sa/3.0)
Conclusion
Valves are critical to the proper operation of hydraulic machinery, and that includes hydraulic final drive motors. The more you know about the basics, the better you can diagnose issue with your hydraulic system.