When you’re out in the field running drilling equipment, you can’t afford to have your hydraulic system break down. The best way to prevent a breakdown is preventative maintenance, and that includes your final drive motors, too. In this Shop Talk Blog post, we are going to talk about maintaining the hydraulic propel motors on your drilling equipment.
Here are a few other blog posts that might be of interest ...
Checking and Changing the Gear Oil
A major cause of problems in propel motors is a failure to maintain sufficient gear oil levels, which is why gear oil levels should be checked regularly. Ideally, you should experience very little loss of gear oil. Signs that you might be running low on gear oil include new noises and vibrations or overheating of the propel motor. If you have to repeatedly top off the gear oil levels, then you have a leak somewhere you need to track down ASAP. If gear oil can leak out, then contamination can get inside.
It is also important to change the gear oil as often your equipment manual recommends. Failure to do so results in a thick, gooey gear oil that does more harm than good.
Follow Up After a Hydraulic Component Fails
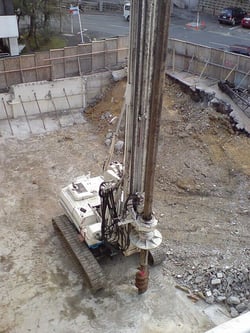
If a hydraulic component such as a pump or final drive fails, it can introduce damaging contamination into the system (e.g., slivers of metal, pieces of damaged seals,etc.). Even after the failed component is replaced, other parts can be damaged by this contamination and result in even more downtime and repairs. When a hydraulic component fails, the hydraulic system needs to be drained and flushed.
Never Ignore Leaks
Leaks mean that fluids, such as hydraulic fluid or gear oil, can make their way out and contaminants can get inside. Hydraulic systems are extremely sensitive to contaminants. Drilling equipment does its job in a dusty environment, and that dust can be very fine. Fine dust can easily makes it way in through leaks in seals or hydraulic lines. Abrasive particles like this can wreak havoc on your hydraulic system, compromising its performance and even leading to catastrophic (and expensive) failures. If you suspect a leak, track down its location and get it repaired ASAP.
Avoid Contaminating the Hydraulic System
The key step to keeping your hydraulic motors on your drill equipment healthy is keeping your hydraulic system as free of contamination as possible. That can be hard in a dusty environment, but it is possible. When you have to open up the hydraulic system, such as when you need to pull a final drive motor, take a few minutes to clean off the area around where the hoses connect. As soon as you disconnect the hoses, cap both the hoses and the connectors to keep dust and debris from getting into the system.
We realize that not all owners and operators have access to a filtering system to make sure that fresh fluid being added is as contaminant-free as possible. However, you can achieve quite a bit by only adding fresh hydraulic fluid to the system and changing the hydraulic filters on your machine according to manufacturer recommendations.
Also, don’t settle for cheap filters. It’s a good idea to use the filters recommended by the manufacturer rather than taking a chance with generic filters that may cause more damage than they prevent.
Conclusion
Drilling rigs, including restricted access drills, shallow exploration drilling units, often includes hydraulic motors as part of their hydraulic system. For those hydraulic motors to provide the performance you need when in the field, they need to be responsibly maintained. They key preventative maintenance tasks to perform include checking and changing the gear oil, following up after a hydraulic component fails, addressing leaks as soon as possible, and being careful to avoid introducing contamination into the system.