Have you ever wondered what kinds of materials are used in excavator buckets? In this Shop Talk Blog post, we are going to talk about the most common materials used in the pins, sides, cutting edge, shell, and teeth of excavator buckets.
Excavator Pins
Excavator pins are usually made of a AISI 4130 or 4140 steel. The AISI 4000 series of steels are chromium molybdenum steels. Chromium improves corrosion resistance and its ability to be hardened while molybdenum increases strength and hardenability, too.
The first digit, 4, represents the class of steel and its major alloying components (in this case, chromium and molybdenum). The second digit, 1, represents the percentage of the alloying elements, which means approximately 1% chromium and molybdenum by mass. The last two digits are the carbon concentration in increments of 0.01%, so AISI 4130 would have 0.30% carbon and AISI 4140 would have 0.40% carbon.
The steel used will most likely have been heat treated using induction hardening. This heat treatment processes produces a hardened surface (58 to 63 Rockwell C) for wear resistance with a ductile interior for toughness. Note that the bushings are often made of the same material as the pins. Some cheaper pins may be made of AISI 1045. This is a medium carbon steel that can be hardened.
Excavator Bucket Sides and Cutting Edges
The bucket sides and cutting edge are usually made of AR steel plate. The most popular grades are AR360 and AR400. AR 360 is a medium carbon, low alloy steel that is heat treated to provide excellent abrasion resistance and high impact strength. AR 400 has also been heat treated but it provides abrasion resistance and superior yield strength. Both of these steels have been carefully quenched and tempered to product qualities that are key to a good bucket. Note that the numbers after AR are the Brinell hardness of the steel.
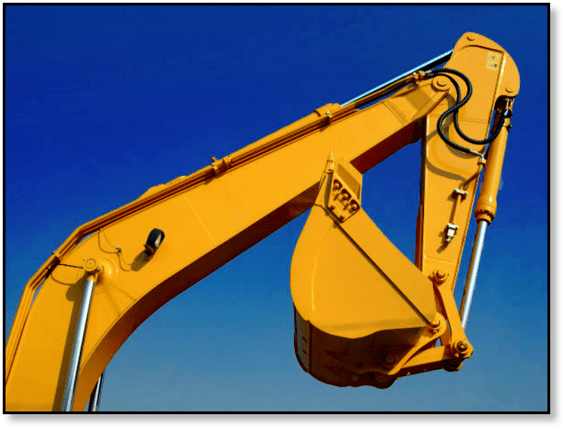
Excavator Bucket Shell
The bucket shell is often made of ASTM A572 Grade 50 (sometimes written A-572-50), a high strength, low alloy steel. This steel is alloyed with columbium and vanadium. Vanadium helps with maintaining the toughness of the steel. This grade of steel is desirable as a bucket shell material because it provides excellent strength without weighing quite as much as comparable steels such as A36. It is also readily welded and formed.
Excavator Bucket Teeth
In order to discuss what bucket teeth are made of, it is important to understand that there are two ways of manufacturing bucket teeth: casting and forging. Cast bucket teeth may be made of a low alloy steel with nickel and molybdenum as the primary alloying elements. Molybdenum improves the hardenability and strength of the steel and can also help minimize some forms of pitting corrosion. Nickel increases strength, toughness, and also helps prevent corrosion. They may also be made from an austempered ductile iron that has undergone heat treatment for wear and impact strength. Forged bucket teeth are also made from a heat-treated alloy steel, but the type of steel varies with manufacturer. The heat treatment improves wear properties and increases impact strength.
Conclusion
Excavator buckets are made from several different materials, but all these materials are types of either steel or iron. The type of material is chosen based on the loading and manufacturing method for that part.
Texas Final Drive is your partner in providing new or remanufactured final drive hydraulic motors from a single mini-excavator to a fleet of heavy equipment. Call today so we can find the right final drive or hydraulic component for you, or check out our online store to find your O.E.M. manufacturer brand motor now.