In this Shop Talk Blog post, we are going to debunk four dangerous myths about undercarriage maintenance for compact track loaders and multi-terrain loaders. These myths include when to replace undercarriage parts, how often the undercarriage should be cleaned, the importance of daily walkarounds, and track tension.
Myth #1: It’s cheaper to put off replacing some undercarriage parts.
Some equipment owners think that putting off the replacement of worn undercarriage parts (e..g, idler wheels or rollers) actually saves them money. This is an in incorrect assumption. When worn out parts are not replaced, they can speed up the wear of other (possibly more expensive) parts. This also applies to parts within the final drive motor (a key component of the undercarriage). Worn out seals or bearings can cause irreparable catastrophic failure if not replaced. Believe it or not, the financially responsible thing to do is to replace worn out undercarriage parts as soon as possible.
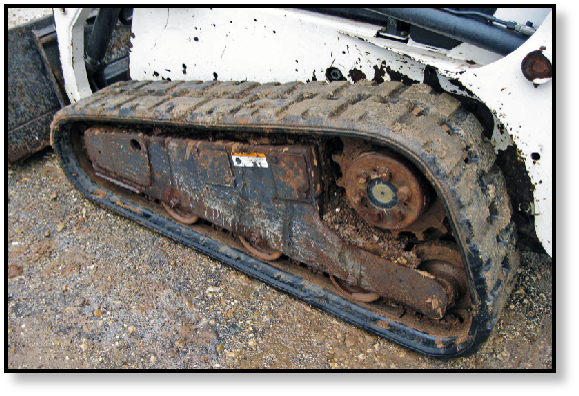
Myth #2: Only OCD people clean their undercarriage daily.
One of the best things you can do for your undercarriage is to take a few minutes to clean it at the end of every work day. You can use a stiff broom to remove material like rocks, wood chips, and chunks of broken concrete. A power washer works really well for loosening packed-in material like mud, clay, or even snow. When this kind of debris is allowed to build up over time, it gets where it’s not supposed to be and causes premature wear to undercarriage components. If packed in tightly enough, it can even displace the main seal on the travel motor, as shown in the image below. If allowed to build up over time, such debris can also add weight to the machine, reducing its fuel efficiency and impacting its performance. Regular cleaning also makes daily walkarounds more effective.
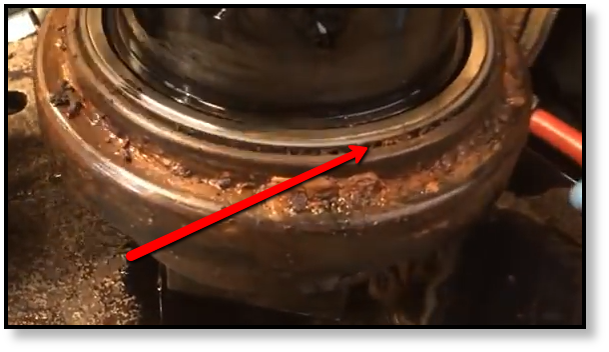
Myth #3: Daily walkarounds are unnecessary.
Daily walkarounds allow problems to be spotted before they turn into expensive repair costs and lengthy down times. Part of a routine inspection includes checking the track tension (both too loose and too tight can accelerate wear), checking the tracks for signs of damage, and applying grease as needed. Also, look over the undercarriage components for signs of uneven or excessive wear and damaged or missing components. Especially focus on the final drive travel motors, sprockets, idlers, and rollers. If you want your equipment to last as long as possible with little downtime and minimal repair costs, take the time to do a daily walkaround.
Myth #4: Track tension doesn’t really make much difference.
Track tension is very important to the life of your undercarriage and all the interacting components that make it up. Loose tracks can speed up the rate of wear and tear on your undercarriage and result in detracking, which is never good thing. Tracks that are too tight, on the other hand, increase the friction acting between the undercarriage components and speed up the rate of wear. The result will be parts that have to be replaced much sooner than normal. Check your owner’s manual for guidelines on what the track tightness should be for different types of working conditions.
Conclusion
Don’t fall for these myths -- take good care of your undercarriage, and it will take good care of your machine so that it keeps running at peak performance, whether you have a Bobcat CLT or a CAT MTL. Never underestimate the impact that the undercarriage has on O&O costs and machine efficiency.
Texas Final Drive is your partner in providing new or remanufactured final drive hydraulic motors from a single mini-excavator to a fleet of heavy equipment. Call today so we can find the right final drive or hydraulic component for you, or check out our online store to find your O.E.M. manufacturer brand motor now.